Solid from the Core: Properties and Applications of Granite
by John Mattke
Interiors & Sources, April 1995
Granite is, quite literally, as old as the earth. It was formed from liquid magma, the molten rock still found at the core of the planet, which was pushed toward the surface to form a substance approaching the hardness and durability of diamond.
Granite is an igneous rock, the name reflecting its fiery beginnings. The chemical composition of granite is similar to that of lava. However, granite owes its hardness and density to the fact that it has been solidified deep within the earth, under extreme pressure. Over the eons, seismic activity has changed the crust of the planet, forcing veins of granite to the surface. Glaciers scraped off layers of dirt, sand and rock to expose granite formations. Typically revealed by outcrops, these deposits have been discovered on every continent.
It is accurate to refer to “granites” in the plural sense, because many varieties of the stone exist. While they differ in color, texture and crystalline structure, the granites have three essential minerals in common:
* Feldspar (50 percent or greater)
* Quartz (25 to 40 percent)
* Mica (three to 10 percent)
These minerals occur in differing proportions, giving each granite its own unique characteristics. Other minerals also may be present in smaller amounts, adding to the variation in color and texture of each granite deposit. As with other natural products, many granites contain a certain amount of grain “movement” or flowing veins in the stone. Many people find this flow and blending of colors to be the most compelling reason for using granite.
Quarrying and Fabrication
Granite has been quarried systematically as far back as 4000 B.C.–long before hardened metals were used. Over the centuries, quarrying techniques evolved very slowly until the 20th century when industrial techniques allowed large quantities of stone to be quarried in a cost effective manner. Low-compression explosives and drive-in quarrying methods are used to remove large blocks of granite from deposits close to the earth’s surface. The granite blocks are then shipped from the quarry by truck or rail to a fabrication facility where they are sawed into slabs of the desired thickness. Each slab is then processed through automatic equipment for the required finish application.
Due to the extreme hardness of granite, much of the fabrication process requires the use of diamond-edge saw blades or a slurry containing diamonds which contributes significantly to the cost of the finished product. However, recent advances in quarrying and fabrication processes have allowed manufacturers to offer many granites at prices equivalent to, and in some cases, less than man-made granite look-alikes and solid surface materials.
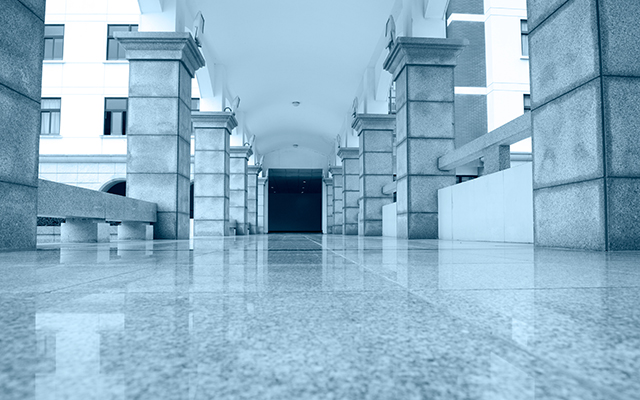
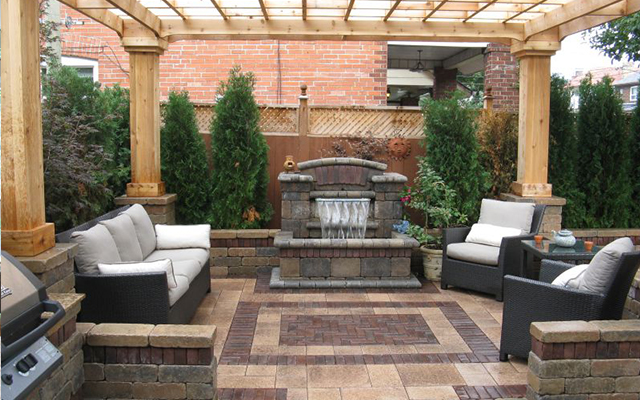
Design Characteristics
The increasing demand for stone use in a wide variety of building applications requires increased knowledge about the different types of stone available and their proper use. The most common are granite, marble, limestone, travertine and sandstone. Each stone has unique physical characteristics which affect its applicability to a specific design. While each type of stone has a place in modern construction, granite and marble are the most often used for interior applications. They both allow for a highly polished surface and provide many beautiful options. They are, however, very different.
Granite is the hardest of all building stones with a very dense grain, making it virtually impervious to stain and uniquely applicable for any interior use. If polished, its high-gloss finish will endure even in harsh environments. These characteristics are ideal for countertops and flooring, making granite a reliable stone for these applications.
Granite also can be provided with a variety of other finishes and, when combined with the vast spectrum of colors available, provide design options surpassing any other type of stone. Granites may contain other minerals providing patterned movement or they may be quarried with consistent grains and little movement.
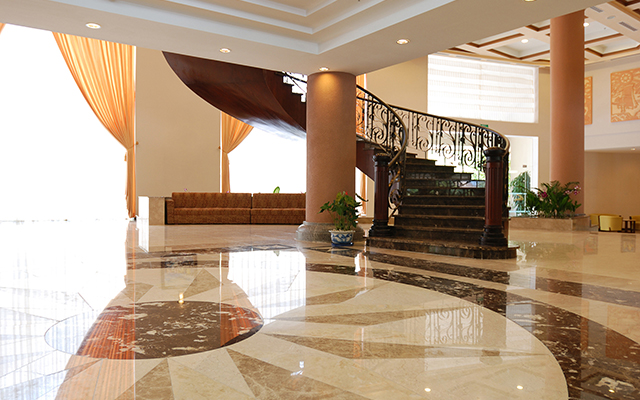
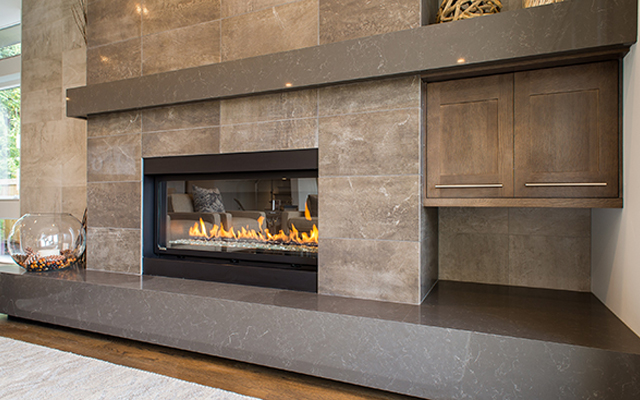
Interior Applications
Today, interior spaces can be as big as all outdoors. Open spaces, greenery, walkways and water blend to provide a comfortable garden look to common areas. Granite is a natural for interior landscaping. As a countertop material, floor and wall covering, stairway, waterfall or planter, granite is durable and clearly a beautiful option.
Two common approaches to granite for wall applications include tile or veneer. Generally, with 3/8- or 1/2- inch granite tile, some flexibility may be sacrificed with regard to piece size, color and finish. Tile can be set with thin-set mortar; no mechanical attachment is used.
Any tile application also can be completed with 3/4 inch or thicker granite veneer. This thicker granite is available in most colors and in a wide variety of piece sizes, allowing for virtually unlimited flexibility. A 3/4-inch veneer is thick enough to permit mechanical attachment which will allow for safe granite use in vertical interior applications.
In recent years, granite has increased significantly in popularity as a residential material. It is used primarily as countertop and flooring material in both single and multiple family housing projects. Part of this popularity results from the recognition of granite countertops, fireplace surrounds and floor tile as a long-term investment. With its deep, iridescent colors, granite offers an elusive, one-of-a-kind beauty created only by nature.
Due to their extreme hardness, second only to diamonds, granite countertops are an ideal work surface. Granite’s polished finish will not wear off and, unlike marble and synthetic countertops, granite will not blister, scratch or crack. It is highly stain resistant and will not become burned or marred if hot pans are set directly on the surface. In fact, because of its cooling characteristics and its extremely smooth, hard surface, countertops made of polished granite are ideal for kneading bread dough.
With the combination of many different countertop edge treatments and the virtually unlimited variety in color, granite countertops and bathroom vanity tops can work beautifully with any design scheme.
Final fabrication and installation of granite countertops should be handled by an experienced, professional stone fabricator. Special equipment and procedures are required to ensure level surfaces, proper jointing and safe handling of granite.
Most granite countertops are fabricated with 1 1/4-inch-thick granite because of its increased vertical slab strength, less chance for breakage and ease of fabrication. Once the slabs are chosen, the fabricator will take care of the necessary cutting for sink holes, corners and any other requirements to achieve a proper fit. The fabricator also will finish the exposed countertop edge according to customer specifications.
If 3/4-inch granite is to be used, a plywood underlayment is attached to increase structural support and a second layer of stone is laminated on the edge of the slab in order to obtain a more substantial looking edge treatment. This lamination occurs prior to edge finishing. Due to the decrease in labor, the overall strength of the thicker material and the relatively minor increase in cost, most home owners prefer the 1 1/4-inch material.
Granite floor tiles may be installed over most sound, level substrates. Granite tiles also may be used for countertops, fireplace surrounds and vanity tops. The method of application will vary to suit the specific type of substrate. Thin granite tiles are installed by tile setters in a manner similar to ceramic tile, using the same setting techniques, materials and tools.
Installations should be performed by experienced installers familiar with the methods and guidelines set forth by the Tile Council of America, Marble Institute of America and the American National Standards Institute. It is important to know that granite flooring often is given a thermal finish, either for aesthetic or safety reasons. This is a flaming process which disintegrates a percentage of the surface crystals, leaving the stone with a rough but uniform finish. Thermal granite tile meets ADA requirements for non-slip surfaces.
Maintenance of Surfaces
Maintenance of granite surfaces is easy. For daily maintenance, a solution of clear, non-sudsing ammonia or a mild neutral detergent and water is recommended. Care should be taken to make sure the detergent is non-abrasive.
On occasion, although granite is very solid and non-porous, spills left on the surface for an extended time period may leave some residual staining. These stains usually dissipate over time on their own. If immediate removal is desired, a simple poultice powder found at most cleaning supply outlets may be used. Additionally, local fabricators can usually provide recommendations regarding extraordinary maintenance should the need arise.
Beauty, design flexibility, durability, value, customer satisfaction–these are the primary advantages of using granite. No matter what the interior application may be, granite will continually look as elegant as the day it was installed. Whenever life-cycle costing formulas are applied, granite is a top performer.